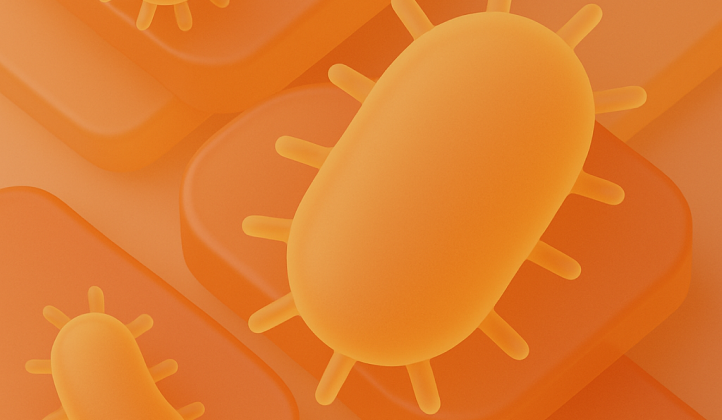
Understanding Alert and Action Limits for Environmental Monitoring
Discover key alert and action limits crucial for effective environmental monitoring. Enhance your strategies and ensure compliance—read the article now!
In pharmaceutical manufacturing, precision isn’t just a target—it’s a requirement. When it comes to Environmental Monitoring (EM), even the slightest deviation can cascade into compliance risks, batch rejections, or regulatory citations. That’s why alert and action levels serve as critical control points in ensuring contamination remains well within acceptable boundaries. Environmental monitoring data plays a crucial role in setting these alert and action levels, helping to identify and respond to deviations from normal operating conditions.
In this blog, we dive into how alert and action levels function, how they are defined, and why they are the cornerstone of any high-performing EM program. This is especially relevant for leaders tasked with ensuring both regulatory compliance and product integrity.
What Are Alert and Action Levels?
Environmental Monitoring generates both microbial and particulate data from cleanrooms. But raw counts aren’t enough—you need predefined thresholds to determine when contamination is becoming a concern. Microbial monitoring data is assessed to determine alert and action levels.
- Alert Levels are early-warning indicators that contamination is increasing but still within acceptable limits. They prompt internal review.
- Action Levels indicate that contamination has exceeded acceptable limits and require documented investigation and corrective action.
These levels apply to both viable (e.g., CFU/m³) and non-viable (e.g., ≥0.5µm particles) data across cleanroom classifications.
New to EM concepts? First, read our Complete Guide to Environmental Monitoring to understand cleanroom classifications, sampling types, and monitoring strategy fundamentals.
How Are Alert and Action Levels Determined?
Traditionally, these thresholds are derived from:
- Regulatory standards like EU Annex 1 and USP < 1116>
- ISO cleanroom classifications (ISO 5 to 8)
- Historical data trends specific to your facility
- Type of process (aseptic vs terminal sterilization)
- Criteria and benchmarks for determining alert and action levels
For example, in a Grade A (ISO 5) cleanroom, even 1 CFU/m³ may be enough to trigger an action. In contrast, Grade C or D environments have higher tolerances.
Alert and action levels should never be static. They must evolve based on:
- EM data trending
- Process modifications
- New equipment or layout changes
- Assessing data trends and process modifications
Why They Matter for Regulatory Compliance
Regulators don’t just check your current values—they want to see:
- How your limits were set
- How often they are reviewed
- How effectively you act on excursions
Adherence to ISO standards helps in setting alert and action levels, ensuring that cleanrooms maintain cleanliness and comply with regulatory requirements.
The updated Annex 1 (2023) puts even greater emphasis on risk-based EM and incident rates over static limits. Action without justification can be viewed as negligence; inaction when thresholds are breached can lead to 483s.
See how FDA inspectors report EM-related failures. Check real Form 483s citing alert/action limit breaches →
Best Practices for Managing Alert & Action Levels
Trending Analysis: Use control charts to visualize contamination behavior.
Root Cause Investigations: Include HVAC logs, gowning audits, material flows.
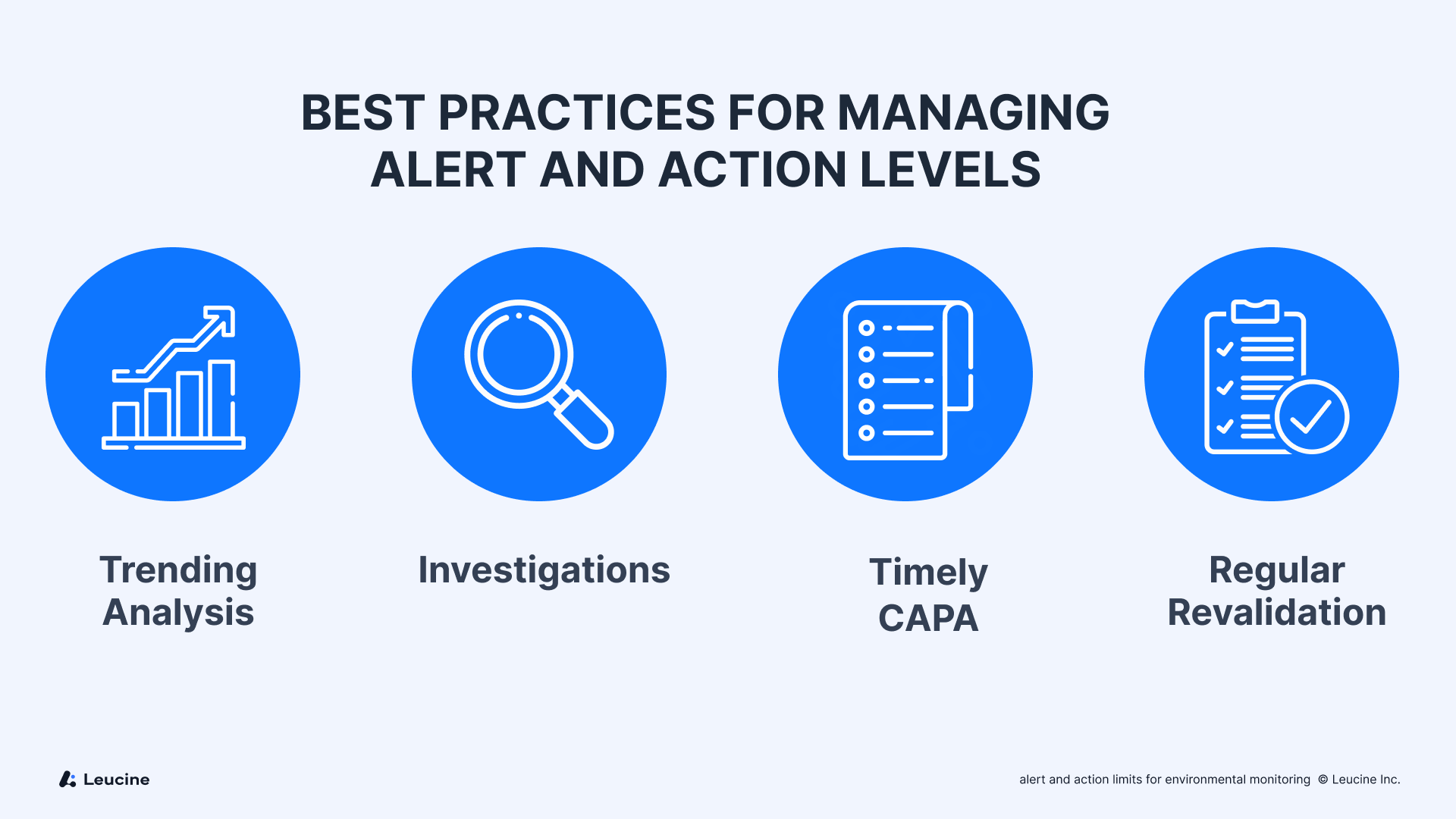
Timely CAPA: Actionable insights need to be documented and resolved quickly.
Regular Revalidation: Ensure that thresholds reflect current risk and data. A proactive approach in managing alert and action levels is crucial for early detection of potential risks, allowing swift corrective actions to maintain product quality and patient safety.
Facilities that tie their alert/action protocols into automated workflows stand out during inspections.
Digitizing Alert & Action Level Control with Leucine
Manual alert tracking via spreadsheets is prone to error and delays. With Leucine’s Environmental Monitoring Software, you can:
- Set facility-specific alert/action thresholds
- Receive real-time alerts with context (zone, trend, operator ID)
- Auto-trigger deviation and CAPA workflows
- Create defensible audit trails with every excursion log
The implementation of digital solutions for alert and action level control is crucial for ensuring accuracy and efficiency in environmental monitoring.
When Do You Investigate an Alert vs Action?
Alert Level: May not always lead to investigation. Used for trending or watchlisting. If frequent, may require SOP review or sampling plan adjustment. Reviewing data regularly is crucial to determine if an alert level warrants further investigation.
Action Level: Investigation is mandatory. Documentation must include:
- Source tracing (personnel, equipment, materials)
- Impact assessment on product or process
- Immediate corrective measures
Delays in investigating action levels are seen as significant compliance risks by both the FDA and EU regulators.
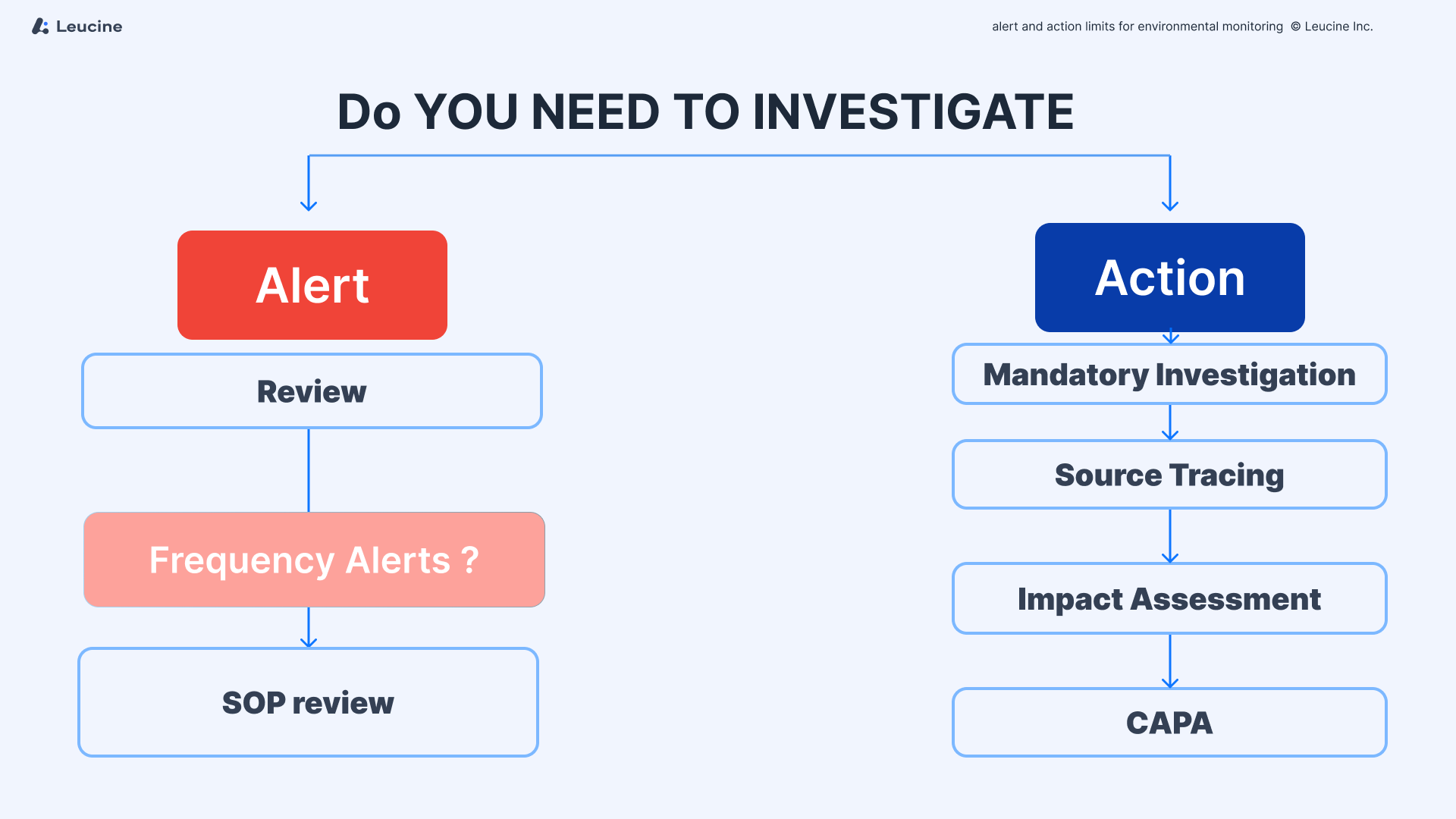
Aligning with Annex 1 Expectations
Annex 1 now requires:
- Incident rate trending instead of just single-limit reference
- Continuous EM in Grade A areas
- Documented justification for EM strategy (location, frequency, response)
Maintaining robust environmental control is crucial for ensuring process stability and preventing contamination. This involves setting alert and action limits as critical thresholds to proactively manage cleanroom environments, ensuring timely interventions and assessments of control systems in response to any deviations from normal conditions.
With rising audit scrutiny, relying on static or outdated alert/action charts is no longer viable.
Build a Robust EM Response System
By integrating environmental monitoring limits into your QMS, you:
- Create traceability across alert, action, investigation, and CAPA
- Reduce resolution time and regulatory risk
- Enhance operational trust and cross-functional visibility
Environmental monitoring programs play a crucial role in maintaining product quality and safety by establishing alert and action limits. These limits are essential for interpreting environmental data and ensuring timely responses to deviations from established standards, ultimately aiding in contamination risk management.
Modern pharma plants operate in real time. Your contamination control strategy should too.
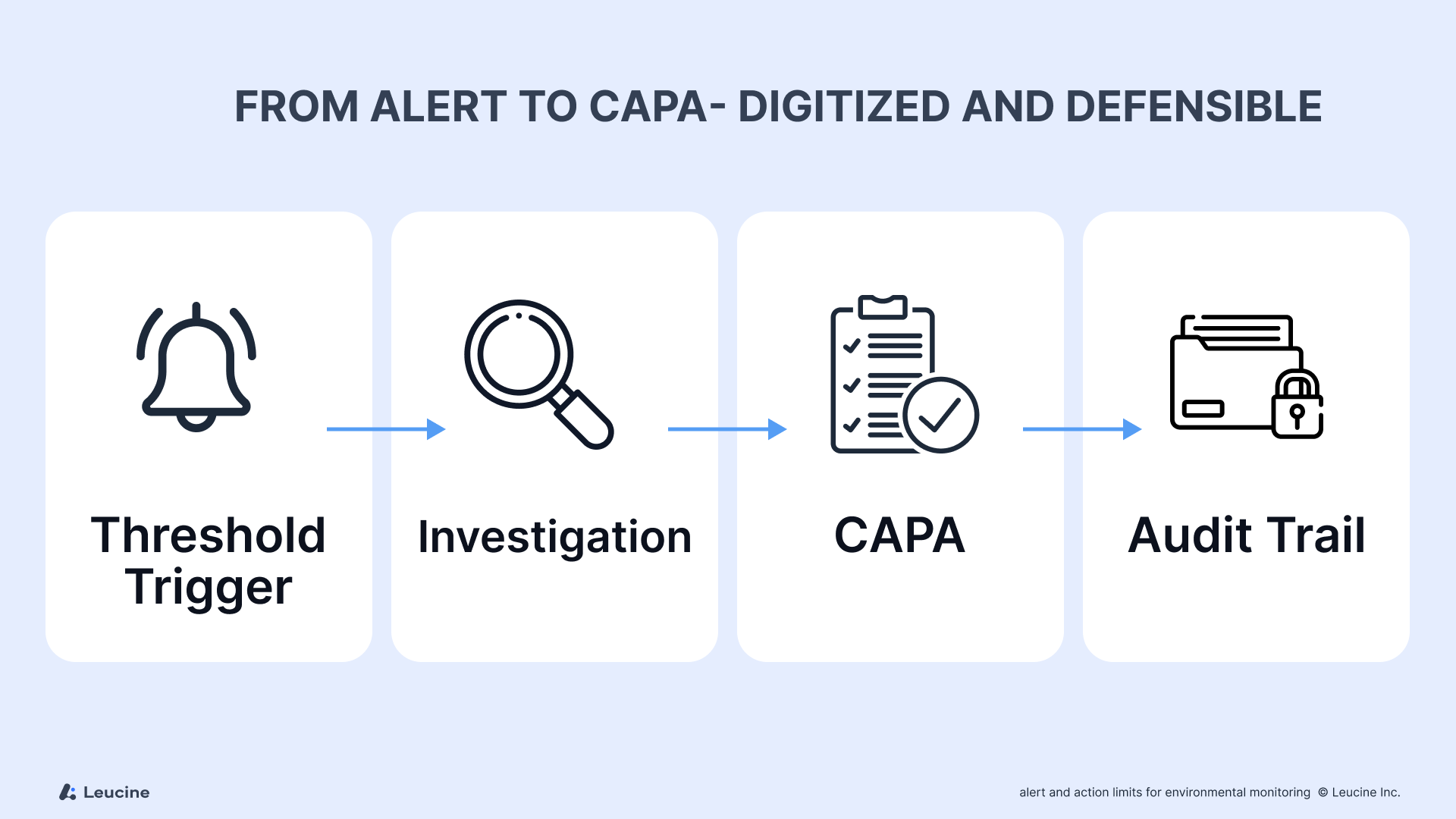
Learn how to implement a full EM strategy with our Pillar Guide to Environmental Monitoring
Conclusion
Alert and action levels in environmental monitoring are more than numbers on a chart. They represent your organization’s ability to detect, respond, and prevent contamination threats. Facilities that treat them as dynamic, data-backed controls stand out not only in audits but in long-term quality outcomes. Implementing robust contamination control strategies is crucial for maintaining compliance with regulatory frameworks like ISO standards and EU GMP guidelines, ensuring product integrity and safety.
Don’t let your EM thresholds be your weakest link. Make them your first line of compliance.
Want to transform how you manage alert and action levels? Talk to our team and see Leucine in action →