Batch Manufacturing Record in Pharmaceutical manufacturing process
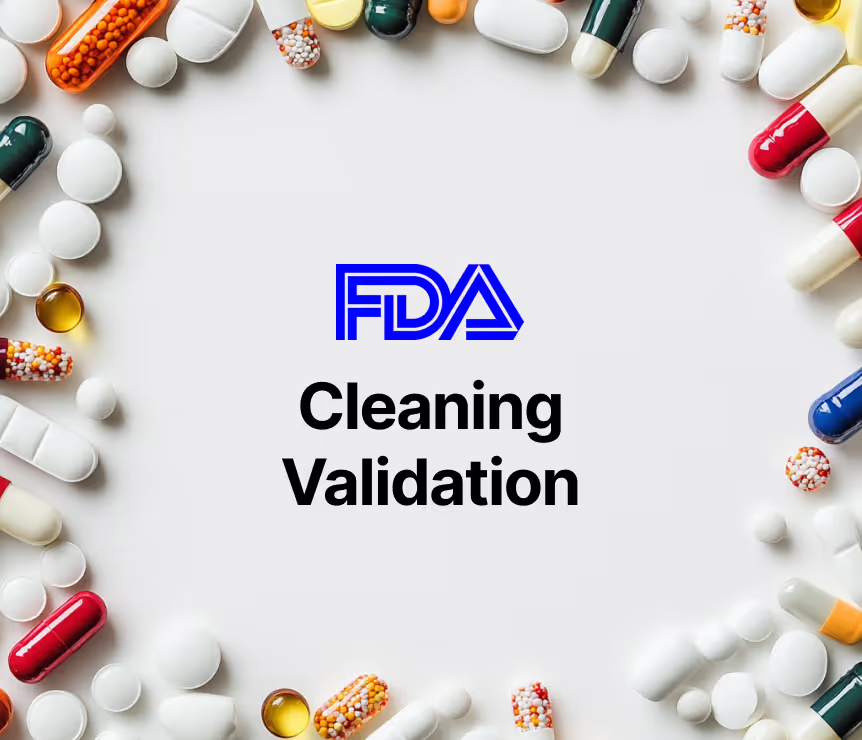
Why BMRs Are the Backbone of Pharma Manufacturing process
In the pharmaceutical industry, where precision and compliance are non-negotiable, Batch Manufacturing Records (BMRs) serve as the backbone of operations. These documents ensure every step of the manufacturing process is traceable, verified, and in strict alignment with regulatory standards, with quality control tests playing a crucial role in ensuring traceability and compliance.
Yet, many pharma professionals face recurring challenges: paper overload, manual errors, and audit risks. For quality leaders and manufacturing heads, these aren’t just annoyances—they’re strategic vulnerabilities. Automated systems can significantly mitigate human error, enhancing accuracy and ensuring compliance. By utilizing batch manufacturing records (BMR), these systems ensure that each record aligns with regulatory standards, thereby maintaining product quality and consistency.
Discover how Leucine’s Batch Execution system eliminates paper overload and strengthens audit readiness. Explore the platform
What Is a Batch Manufacturing Record?
A Batch Manufacturing Record (BMR) is a comprehensive, chronological record that documents the complete history of a specific batch process—from raw materials to final release, including essential batch details such as the batch name, identification number, and quantity. Accurate data entry is crucial in maintaining comprehensive records, as it enhances accuracy and consistency, minimizes human error, and reduces reliance on manual documentation.
BMR vs. BPR vs. MFR
- BMR (Batch Manufacturing Record): Documents real-time batch production data.
- BPR (Batch Production Record): Often used interchangeably with BMR, but may emphasize production aspects more. Batch production records (BPRs) are essential documentation in manufacturing processes, tracking actual production details such as equipment settings and personnel involved. Unlike BMRs, which are prescriptive, BPRs serve as logs of the production journey, crucial for ensuring compliance and optimizing manufacturing operations.
- MFR (Master Formula Record): The predefined recipe or protocol that guides each BMR. The MFR, also known as the master production record, is a crucial document that serves as the highest-level batch record outlining the manufacturing processes and instructions for a product. It ensures consistency in production and compliance with regulations.
BMRs sit at the core of the pharmaceutical production lifecycle, ensuring every unit of product adheres to cGMP requirements and quality standards. For example, FDA warning letters often cite poor documentation practices—underscoring the need for accurate, complete batch records to avoid regulatory violations. Accurate documentation is essential for meeting regulatory requirements, ensuring product safety and consistency.

What Should Be Included in a BMR?
An effective BMR includes detailed, real-time data that ensures full traceability of the finished product and audit readiness, enabling swift issue resolution and seamless integration into digital manufacturing systems. It should cover product details like name, batch number, dosage form, and strength; the list and source of raw and intermediate materials; a step-by-step outline of the manufacturing process; and identification of operators and equipment used. Additionally, a batch packaging record should be included to outline the detailed packaging processes for specific products, including components, packaging instructions, and required quality assurances. Additional components include quality control test results, records of deviations and corrective actions, and final yield along with release signatures. Stability testing is crucial in maintaining product quality, ensuring compliance with ICH guidelines. Quality assurance representatives must verify and sign all batch records to ensure accuracy and adherence to regulatory standards.
Get our free BMR checklist to audit your current process. Download now
Benefits of an Accurate BMR in Pharmaceutical manufacturing process parameters
Pioneering intelligent solutions begins with flawless documentation, which is crucial for an efficient production workflow. Accurate BMRs are essential for GMP compliance (as per 21 CFR Part 211 and EU GMP Annex 11), ensuring traceability for potential recalls, improving QA/QC transparency, and reducing the risk of production errors such as mix-ups and cross-contamination. Additionally, accurate BMRs enhance product quality by reducing errors and ensuring compliance with regulatory standards.

Common BMR Mistakes & FDA 483 Triggers
Even minor mistakes in BMRs can lead to serious regulatory consequences. Common pitfalls include incomplete or Missing entries, Falsified or backdated signatures, Illegible handwriting, and Deviations that are undocumented or poorly documented. Manual data entry can introduce errors that compromise data integrity and lead to compliance issues. Avoiding these errors is crucial for maintaining inspection readiness and avoiding FDA 483 observations. A robust documentation process ensures compliance, consistency in production, and quality control, which are essential for accurate manufacturing records.
Going Digital: Why Pharma Is Shifting to Electronic BMRs
Given the frequency and severity of documentation errors highlighted earlier, it becomes clear that traditional methods can no longer keep up. Paper-based systems are increasingly obsolete. Here’s why digital transformation with electronic batch records is imperative:

- Challenges with paper BMRs: Prone to error, delays, loss, and inefficiencies
- Features of robust EBR software:
- Real-time deviation alerts
- Approval workflows
- MES/QMS/ERP integrations
- 21 CFR Part 11 compliance
Electronic systems help in reducing human error and improving accuracy, ensuring compliance and operational efficiency. Additionally, they contribute to a more efficient production workflow by streamlining procedures and supporting batch manufacturing processes.
How to Prepare a GMP-Compliant BMR (Step-by-Step)
Creating a GMP-compliant Batch Manufacturing Record is more than a procedural task—it’s a strategic practice that ensures quality, traceability, and regulatory alignment throughout the production lifecycle. Preparing batch manufacturing records involves selecting BMR software tailored for the chemical and process manufacturing industry, emphasizing features that facilitate compliance, security, inventory management, quality control, and integration with manufacturing equipment. Detailed instructions are crucial in this process to ensure compliance with quality control procedures and regulatory standards. Recording in process testing results is also essential for compliance and quality control, as it monitors the product throughout the manufacturing process and checks for any anomalies. Here’s a comprehensive step-by-step approach:

1. Draft the Master BMR Template
- Base it on the Master Formula Record (MFR) which outlines the standardized manufacturing process.
- Ensure inclusion of product-specific details such as batch size, dosage form, and manufacturing method.
- Structure the template to align with applicable SOPs, cGMP guidelines, and internal quality standards.
- Include master packaging records to ensure compliance during the packaging of bulk finished products into various forms, such as tablets or capsules.
- Emphasize the role of BMR software in creating master packaging records (MPR) and batch packaging records (BPR) as essential documentation for packaging procedures, especially in industries like pharmaceuticals.
2. Link Relevant Control Documents
- Integrate Standard Operating Procedures (SOPs), quality specifications, and test methods directly into the BMR.
- Ensure these references are up-to-date, version-controlled, and accessible to authorized personnel.
- This linkage reduces ambiguity and supports consistency in execution and verification, which is essential for maintaining regulatory compliance.
3. Set Up Review and Approval Workflows
- Route the draft BMR for cross-functional review—typically by QA, QC, Production, and Regulatory Affairs.
- Capture digital signatures and timestamps to maintain an audit trail.
- Document the personnel involved in the review and approval process to ensure compliance with regulatory standards.
- Use predefined workflows in Electronic BMR systems to automate reminders and prevent delays.
4. Enable Real-Time Data Capture and Verification
- Design sections for in-process checks, critical process parameters (CPPs), and test results to be recorded in real-time.
- Use barcode/RFID integrations or mobile interfaces to streamline operator inputs and reduce manual errors.
- Integrate process manufacturing equipment, such as scales and thermometers, to automate data entry and improve accuracy in managing complex formulations.
- Embed deviation logging mechanisms to flag and manage anomalies immediately.
- Include details about health and safety hazards and necessary personal protective equipment (PPE) for each step of the manufacturing process to ensure compliance and worker safety.
5. Archive and Retrieve Securely
- Store completed BMRs in a validated electronic document management system (EDMS).
- Ensure the system supports searchability, version history, and audit readiness.
- Set access permissions and retention policies in line with 21 CFR Part 11 and local GMP expectations.
- Document storage conditions within batch manufacturing records and master formula records to maintain product quality and efficacy throughout their shelf life.
Simplify review cycles by enabling automated batch release workflows that reduce approval time and human error.
Choosing the Right Batch Record Software solutions
Selecting the right BMR software for process manufacturing is a strategic decision. Key considerations include whether the platform complies with 21 CFR Part 11, supports audit trails, offers role-based access, and integrates with other manufacturing systems. Additionally, evaluate if it scales across multiple sites and delivers measurable ROI by reducing audit risks, enhancing efficiency, and ensuring documentation accuracy.
It is also crucial to choose software tailored for the chemical and process manufacturing industries, as it can enhance accuracy, efficiency, and adherence to quality standards in production.
Conclusion
Batch Manufacturing Records are not just compliance tools—they are strategic assets. By ensuring traceability, consistency, and accountability, they enable pharma manufacturers to achieve operational excellence.
Now is the time to innovate. Digital BMRs are no longer optional—they're the cornerstone of modern GMP.
Let’s pioneer your digital transformation journey with precision and purpose. Get started with Leucine
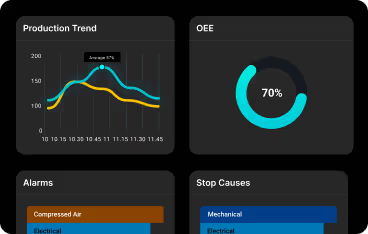
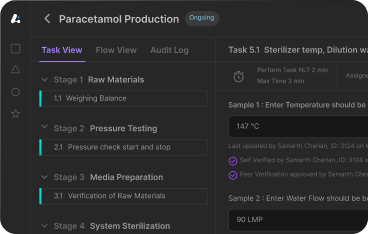
