Master Batch Record in Pharma
Discover how a master batch record ensures GMP compliance, process consistency, and quality in pharma manufacturing with Leucine’s digital MBR toolkit.
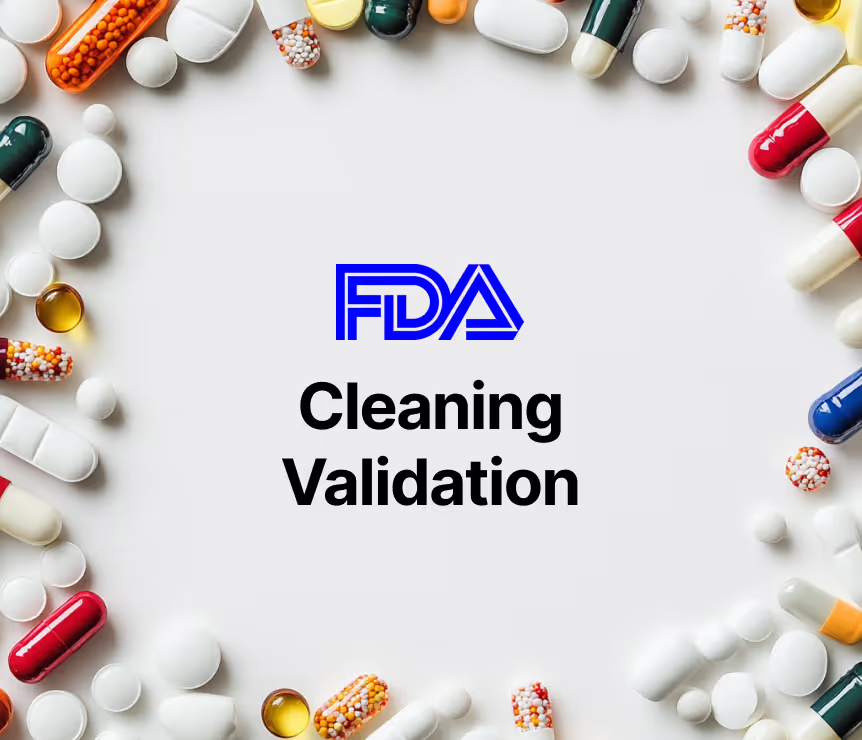
What is a Master Batch Record (MBR)?
In the realm of pharmaceutical manufacturing, precision begins with the Master Batch Record (MBR)—a foundational document that governs the entire batch production process. Think of it as the blueprint for operational excellence, designed to ensure consistency, compliance, and control across every production run.
An MBR defines:
- The formulation, equipment, and procedures to be used
- Critical process parameters to monitor
- The quality specifications that every batch must meet
A streamlined approval process is crucial in ensuring the accuracy and regulatory compliance of the MBR, minimizing errors, and facilitating timely production scheduling.
It is created before any manufacturing begins and is used to generate the Batch Production Record (BPR) or Batch Manufacturing Record (BMR) for each specific lot. MBRs also include specifications for quality control tests, which are essential for regulatory compliance and maintaining product quality throughout the manufacturing process. Without an accurate MBR, even the most sophisticated pharma systems risk deviation, inefficiency, or regulatory non-compliance.
Lay the foundation for flawless executio. Explore Leucine’s Master Batch Record toolkit
Enhance your understanding of FDA-compliant batch records to maintain consistency across all production batches.
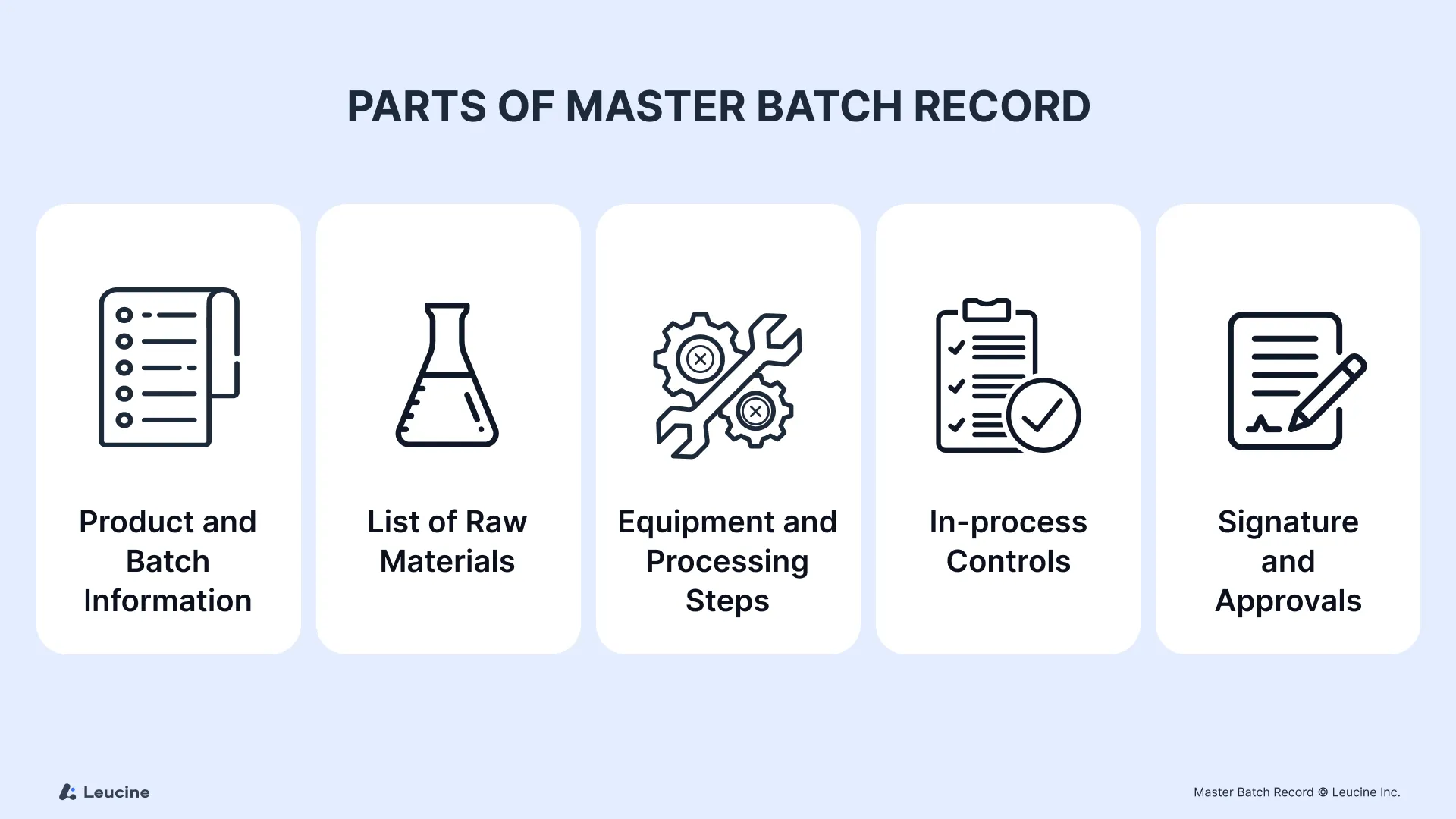
Key Components of a Master Batch Record
A well-crafted MBR is more than a document—it’s a control mechanism that bridges product development with GMP-compliant execution. To achieve strategic excellence through innovation, each component must be defined with accuracy and foresight. The MBR is one of the crucial documents required for regulatory compliance in the pharmaceutical industry.
Here’s what a complete MBR should include:
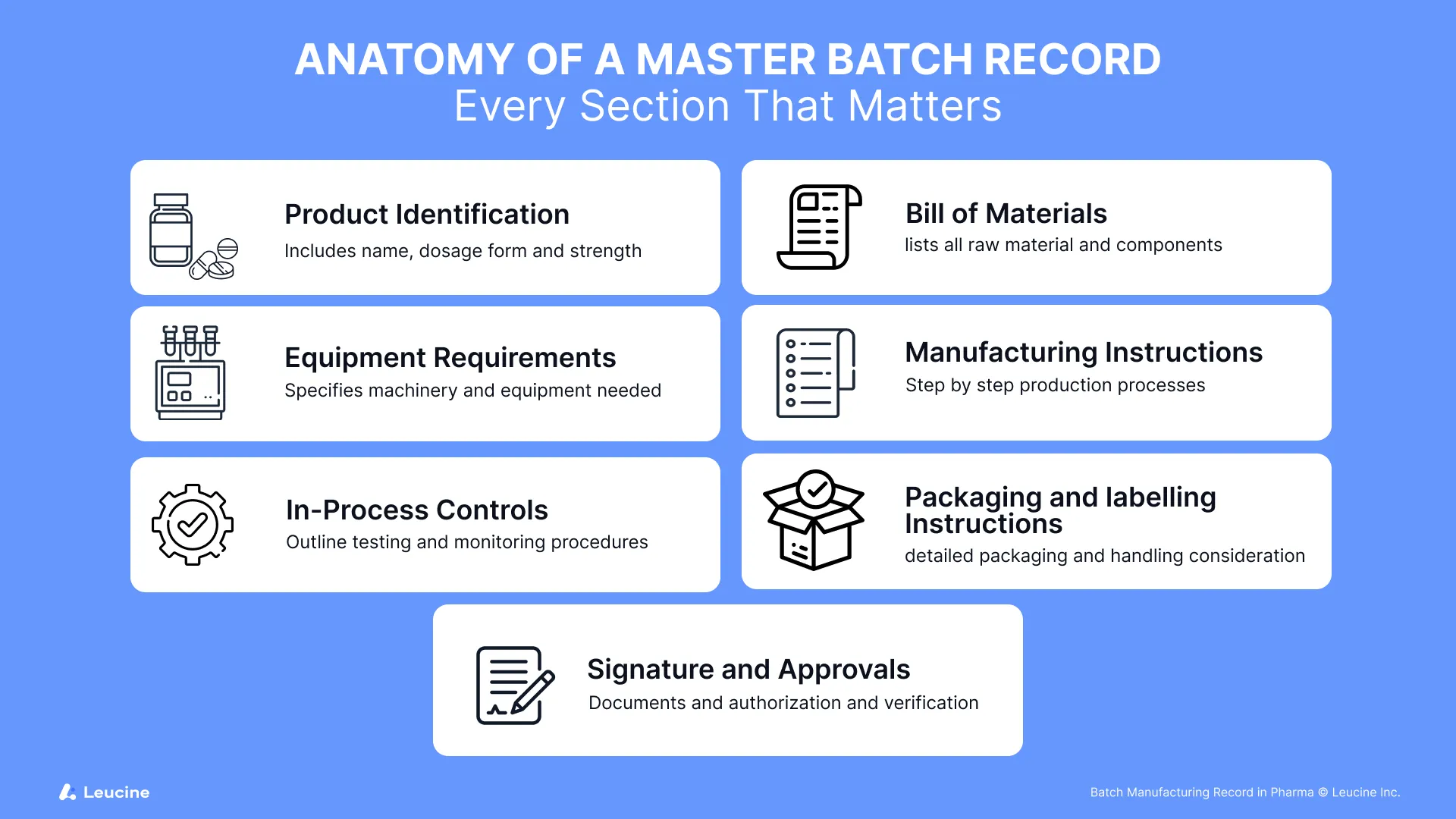
1. Product Identification
- Product name, dosage form, strength, and intended batch size
- Product code or manufacturing license reference
- Batch number: Batch numbers are crucial for documenting the execution of manufacturing processes. They play a key role in Batch Production Records (BPR) and Batch Packaging Records (BPR), ensuring compliance with regulatory requirements and maintaining quality control throughout the production and packaging stages.
2. Bill of Materials (BoM)
- Complete list of active pharmaceutical ingredients (APIs) and excipients
- Material codes, quantities, and quality grade requirements
3. Equipment Requirements
- Specific equipment and tools needed for each step
- Calibration and cleaning requirements linked to SOPs
4. Manufacturing Instructions
- Chronological step-by-step procedures with detailed instructions
- Defined operating ranges for temperature, pressure, mixing speed, etc.
5. In-Process Controls
- Test parameters to monitor during manufacturing
- Identifying and monitoring critical quality attributes is essential to ensure product quality and consistency. These attributes need to be controlled during the manufacturing process to maintain adherence to required standards.
- Acceptance criteria, acceptable limits, and sampling instructions
6. Packaging & Labeling Instructions
- Type of packaging materials and labeling format
- Special storage or handling considerations
7. Signatures & Approvals
- Review and authorization by QA/QC, manufacturing, and regulatory personnel
Maintaining compliance records is crucial for documenting the approval process and ensuring regulatory compliance.
Transform with precision—ensure every record is audit-ready from the start. See Leucine in action
Master Batch Record vs. Batch Production Record: What’s the Difference?
While often confused or used interchangeably, the Master Batch Record (MBR) and Batch Production Records (BPRs) (sometimes also referred to as Batch Manufacturing Record - BMR) serve distinct roles within pharmaceutical manufacturing.
Documentation in pharmaceutical manufacturing is critical for regulatory compliance, quality assurance, and risk management. Master batch records (MBRs) are essential documentation to ensure consistency and traceability in manufacturing processes, aligning with the principles of current Good Manufacturing Practices (cGMP).
Let’s break it down:
Think of the MBR as the architect’s blueprint, while the BPR is the construction logbook. Both are essential to ensure that the product is built as intended—and that any variances are tracked and explained.
Ensure blueprint and execution align—see how Leucine bridges MBR to BPR seamlessly. Learn more
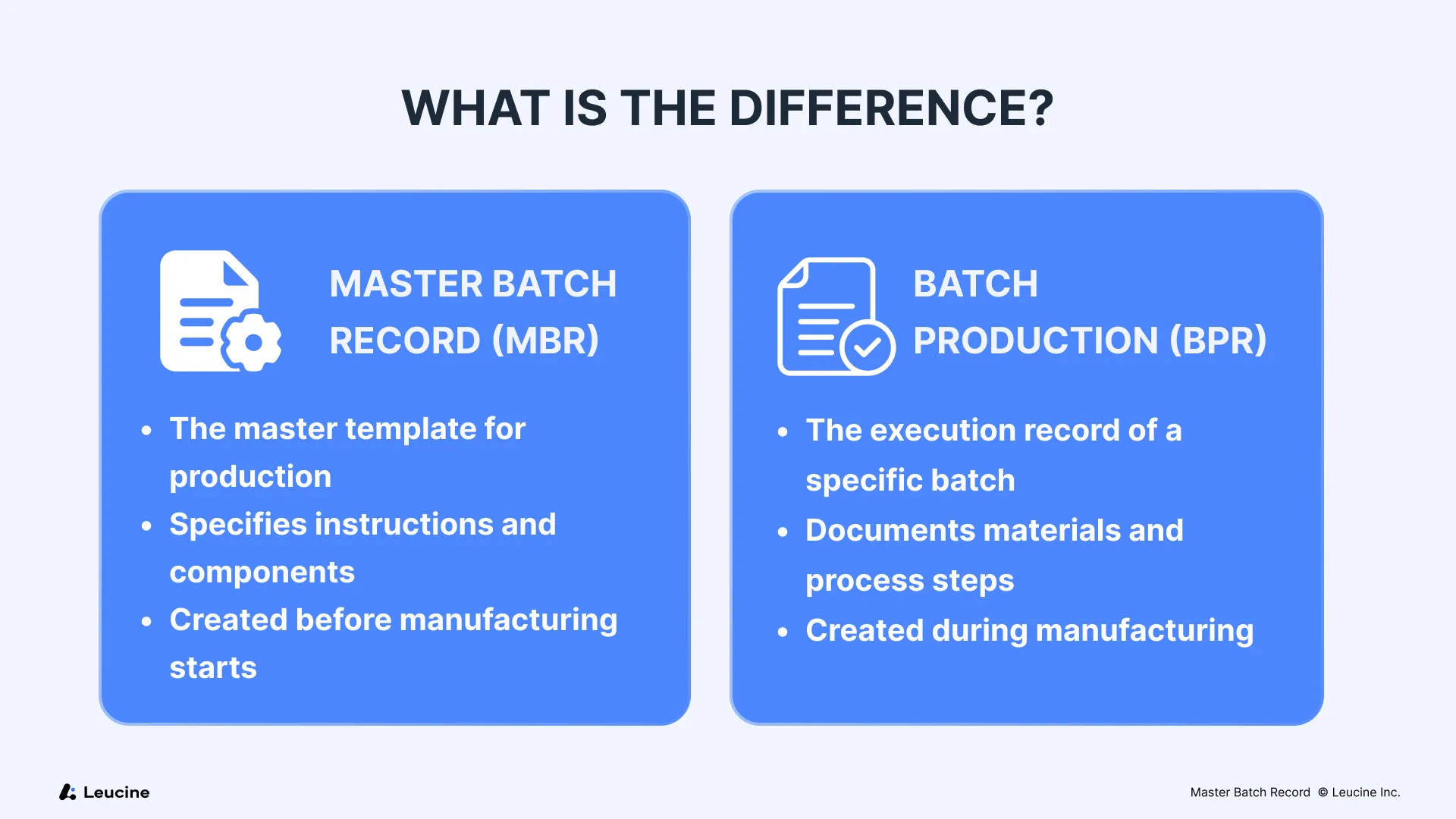
Regulatory Guidelines for Master Batch Records (FDA, WHO, EU GMP)
A Master Batch Record isn’t just an internal best practice—it’s a regulatory imperative across global pharmaceutical markets, essential for meeting regulatory requirements. Whether you’re operating under FDA, WHO, or EU GMP oversight, MBRs must meet strict documentation and process control requirements to ensure Good Manufacturing Practices (GMP) are upheld.
In the life sciences industry, stringent regulatory requirements necessitate detailed documentation and compliance records to ensure product safety and effectiveness. MBRs play a crucial role in detailing procedures and specifications necessary to meet quality standards, which are mandated by regulatory authorities such as the FDA and EMA, thereby safeguarding the quality and purity of pharmaceutical products.
FDA (21 CFR Part 211 – Subpart J & F)
- Requires a written MBR for each drug formulation and batch size.
- Must include component quantities, equipment, processing instructions, in-process controls, and labeling instructions.
- Every BPR must be checked against the approved MBR to ensure accuracy.
WHO GMP Guidelines
- Emphasize the importance of MBRs in maintaining product quality, reproducibility, and traceability.
- The MBR must be authorized, dated, and signed by responsible personnel before issuance.
🇪🇺 EU GMP – Annex 15 & Part I
- Stresses the validation of manufacturing processes and the role of MBRs in maintaining consistent batch quality.
- Requires that changes to MBRs follow a controlled document management and review process.
Failing to maintain accurate and approved MBRs is a frequent cause of FDA 483s and EU GMP non-conformities—highlighting the need for a system that ensures real-time control and change management.
Check 2025 guidelines on Batch manufacturing : Batch Manufacturing Record Guidelines in the Pharmaceutical Industry
Common Errors in MBRs and How to Avoid Them
Even a minor lapse in a Master Batch Record can cascade into compliance violations, batch rejections, or regulatory findings. Quality assurance plays a critical role in preventing these errors by ensuring that each batch meets established quality standards and compliance requirements. To uphold strategic excellence through innovation, manufacturers must proactively mitigate risks by understanding the most frequent errors and how to avoid them.
- Manual data entry: Relying on manual data entry increases the risk of human errors and compromises data integrity. Transitioning to digital solutions can significantly reduce these risks and improve overall efficiency.
Frequent MBR Mistakes:
- Ambiguous instructions: Vague language or missing parameters in procedures can result in inconsistent execution.
- Unapproved document versions: Using outdated templates leads to deviations from validated processes.
- Omitted in-process controls: Skipping QC checkpoints undermines batch integrity and traceability.
- Incomplete equipment specifications: Not documenting calibration or cleaning instructions can trigger cross-contamination risks.
- Non-compliant approval workflows: Missing signatures or unauthorized personnel approvals invalidate the MBR.
How to Avoid Them:
- Standardize authoring with templates tied to SOPs and controlled vocabularies.
- Automate version control using electronic systems with access restrictions and audit trails.
- Integrate real-time QA inputs during the MBR preparation process to ensure in-process compliance.
- Leverage role-based access for approvals to ensure sign-offs align with regulatory roles.
- Train teams continuously on GMP expectations and documentation discipline.
Protect your process with precision—explore Leucine’s built-in controls for MBR quality. Audit your documentation process
Importance of MBRs in GMP Compliance
A Master Batch Record is far more than a procedural document—it’s a cornerstone of GMP compliance. Quality control plays a crucial role in GMP compliance by ensuring that MBRs and manufacturing processes meet specified quality standards. Regulators expect not only the presence of MBRs but also evidence that they are accurate, controlled, and consistently followed to ensure compliance. In this context, the MBR becomes a strategic safeguard against variability, risk, and non-compliance.
Streamline your operations with automated batch release processes that align with FDA expectations.
Here’s why MBRs are critical to Good Manufacturing Practice:
1. Consistency Across Batches
By standardizing every critical instruction and control point, MBRs ensure uniformity in product quality across all production runs—crucial for both efficacy and safety.
2. Traceability & Accountability
A well-structured MBR defines who is responsible for each step in the process, enabling full traceability from raw materials to finished product release.
MBRs play a crucial role in ensuring data integrity throughout the pharmaceutical manufacturing process by documenting critical manufacturing parameters and quality control tests, thereby maintaining accuracy and traceability, which are essential for compliance with GAMP 5 guidelines.
3. Inspection Readiness
During regulatory inspections, MBRs serve as evidence of GMP alignment, demonstrating process control, proper documentation practices, and timely deviation management.
4. Foundation for Continuous Improvement
MBRs provide historical insights into production behavior and deviations—allowing data-driven enhancements to SOPs, formulations, and equipment setups.
Digitizing Master Batch Records: Benefits of eMBRs
In an era where data integrity and process agility are non-negotiable, the shift from paper-based MBRs to electronic batch records is not just a trend—it’s a strategic leap forward. By leveraging digital technologies, pharma manufacturers can overcome the inefficiencies and risks of manual documentation, enabling precision, speed, and compliance at scale. The challenges associated with using paper-based records include complexities in compliance documentation and increased human errors, whereas transitioning to digital solutions can improve data integrity and streamline compliance processes. Advanced software solutions provide benefits such as workflow automation, regulatory compliance, and integration with other quality management systems, ultimately enhancing efficiency and quality assurance.
Key Benefits of eMBRs:
1. Real-Time Process Control
- Digital instructions, checkpoints, and deviation alerts help ensure that GMP protocols are followed exactly, every time.
- Operators are guided through workflows step-by-step, reducing reliance on memory or manual interpretation.
2. Error Reduction & Data Integrity
- No more illegible handwriting, missing fields, or unapproved edits.
- Every action is recorded with timestamps, user IDs, and traceable audit trails—supporting 21 CFR Part 11 compliance.
3. Faster Review and Release
- Automated notifications and digital sign-offs streamline the approval chain.
4. Integration with Enterprise Systems
- Seamless links to MES, QMS, LIMS, and ERP allow for end-to-end traceability and data flow—from raw material intake to final product release.
5. Scalability and Global Consistency
- Standardized MBRs across facilities reduce variability and ensure consistent compliance—even across global manufacturing networks.
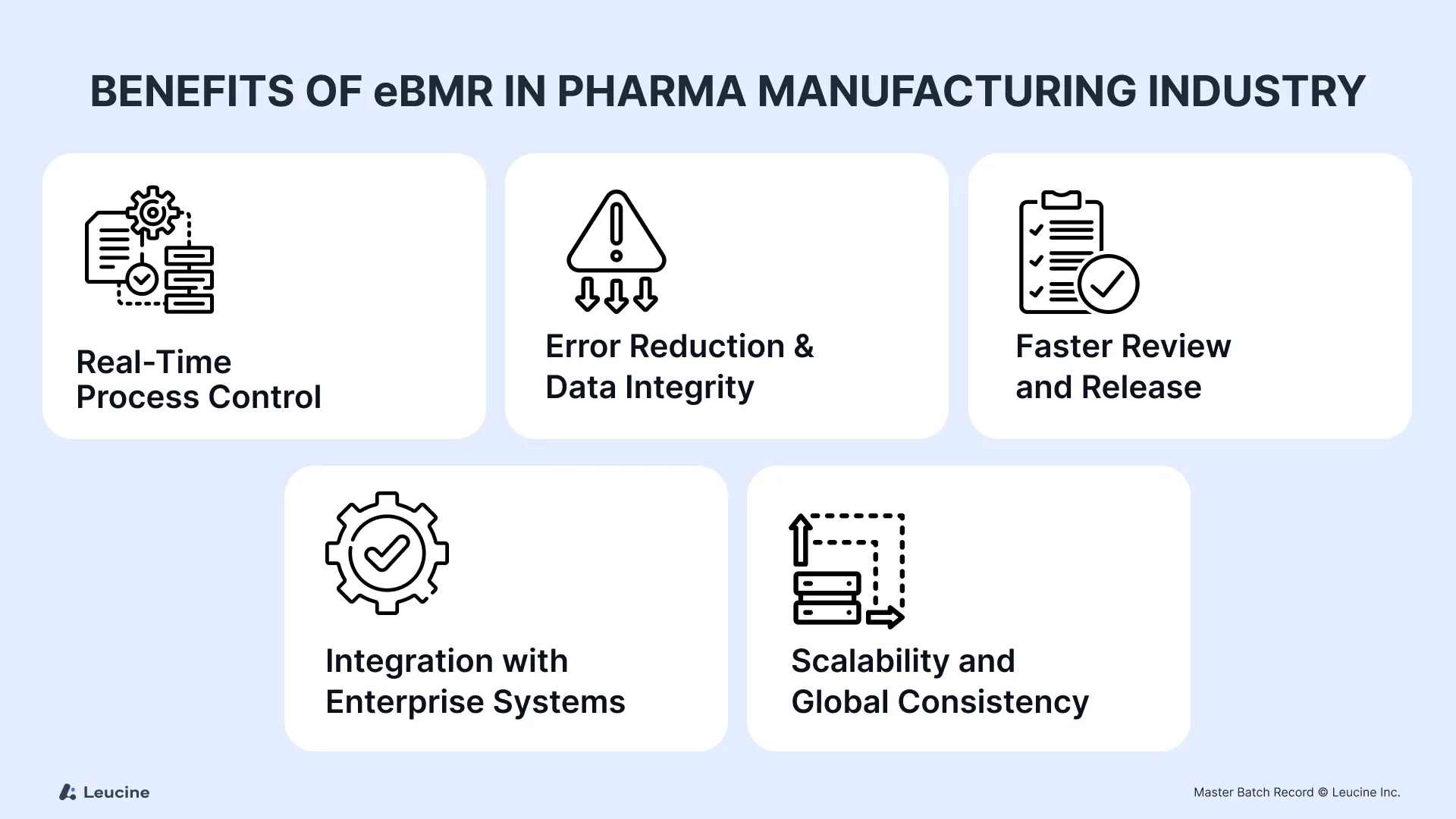
How Leucine Can Help Manage Your Master Batch Records
At Leucine, we believe that the future of pharmaceutical manufacturing lies in intelligent, compliant, and connected operations. That’s why our platform is built to transform MBR management with precision and strategic depth—from creation to execution. Pharmaceutical companies need effective MBR management to ensure regulatory compliance and efficient document handling.
Here’s how Leucine enables pharma leaders to take control of their Master Batch Records:
- Smart Authoring & Version Control: Leucine integrates seamlessly with existing quality systems, providing automated data exchange, real-time reporting, and compliance with regulatory standards. This ensures that your MBRs are always up-to-date and accurate.
Seamless Integration Across Systems
- Connect your MBRs to MES, QMS, LIMS, and ERP systems to enable real-time visibility and data flow throughout the batch lifecycle.
AI-Driven Compliance Intelligence
- Detect anomalies, missing steps, or compliance gaps proactively with AI-powered insights.
- Use historical data trends to optimize processes and reduce recurring deviations.
End-to-End Digital Execution
- Automatically generate BMRs from approved MBRs.
- Guide operators through digital workflows with embedded instructions, reducing training time and execution risk.
Audit-Ready Documentation
- Built-in support for 21 CFR Part 11, Annex 11, and WHO GMP requirements.
- Every action is recorded with timestamps, digital signatures, and audit trails—ensuring inspection readiness 24/7.
Let’s pioneer your digital transformation journey with precision and purpose. Book your personalized demo today